Little Pharma on the Prairie
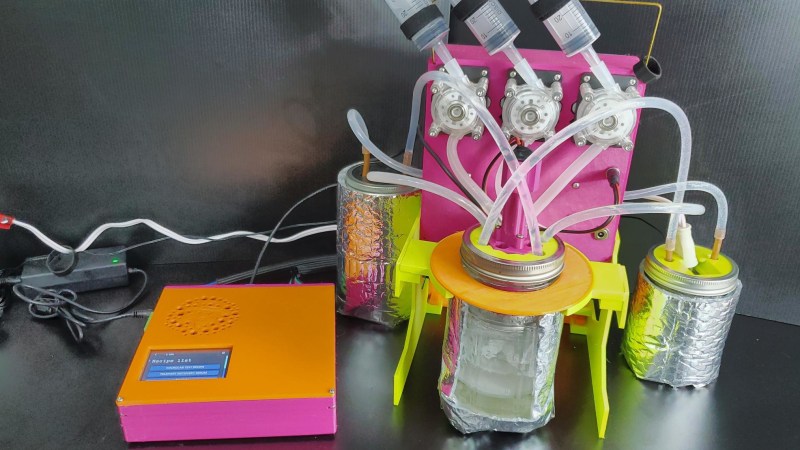
Let’s get the obvious out of the way first — in his DEFCON 32 presentation, [Dr. Mixæl Laufer] shared quite a bit of information on how individuals can make and distribute various controlled substances. This cuts out pharmaceutical makers, who have a history of price-gouging and discontinuing recipes that hurt their bottom line. We predict that the comment section will be incendiary, so if your best argument is, “People are going to make bad drugs, so no one should get to have this,” please disconnect your keyboard now. You would not like the responses anyway.
Let’s talk about the device instead of policy because this is an article about an incredible machine that a team of hackers made on their own time and dime. The reactor is a motorized mixing vessel made from a couple of nested Mason jars, surrounded by a water layer fed by hot and cold reservoirs and cycled with water pumps. Your ingredients come from three syringes and three stepper-motor pumps for accurate control. The brains reside inside a printable case with a touchscreen for programming, interaction, and alerts.
It costs around $300 USD to build a MicroLab, and to keep it as accessible as possible, it can be assembled without soldering. Most of the cost goes to a Raspberry Pi and three peristaltic pumps, but if you shop around for the rest of the parts, you can deflate that price tag significantly. The steps are logical, broken up like book chapters, and have many clear pictures and diagrams. If you want to get fancy, there is room to improvise and personalize. We saw many opportunities where someone could swap out components, like power supplies, for something they had lying in a bin or forego the 3D printing for laser-cut boards. The printed pump holders spell “HACK” when you disassemble them, but we would have gone with extruded aluminum to save on filament.
Several times [Mixæl] brings up the point that you do not have to be a chemist to operate this any more than you have to be a mechanic to drive a car. Some of us learned about SMILES (Simplified Molecular Input Line Entry System) from this video, and with that elementary level of chemistry, we feel confident that we could follow a recipe, but maybe for something simple first. We would love to see a starter recipe that combines three sodas at precise ratios to form a color that matches a color swatch, so we know the machine is working correctly; a “calibration cocktail,” if you will.
If you want something else to tickle your chemistry itch, check out our Big Chemistry series or learn how big labs do automated chemistry.