Modular Multi-Rotor Flies Up To Two Hours
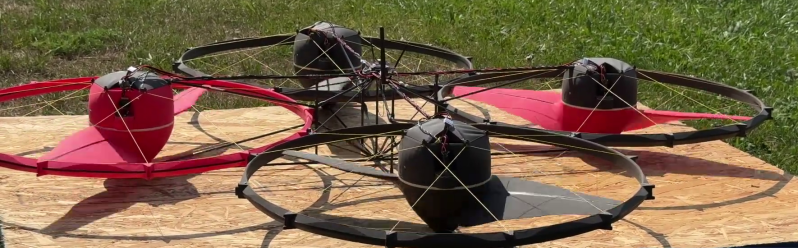
Flight time remains the Achilles’ heel of electric multi-rotor drones, with even high-end commercial units struggling to stay airborne for an hour. Enter Modovolo, a startup that’s shattered this limitation with their modular drone system achieving flights exceeding two hours.
The secret? Lightweight modular “lift pods” inspired by bicycle wheels using tensioned lines similar to spokes. The lines suspend the hub and rotor within a duct. It’s all much lighter than of traditional rigid framing. The pods can be configured into quad-, hex-, or octocopter arrangements, featuring large 671 mm propellers. Despite their size, the quad configuration weighs a mere 3.5 kg with batteries installed. From the demo-day video, it appears the frame, hub, and propeller are all FDM 3D printed. The internal structure of the propeller looks very similar to other 3D-printed RC aircraft.
The propulsion system operates at just 1000 RPM – far slower than conventional drones. The custom propellers feature internal ring gears driven by small brushless motors through a ~20:1 reduction. This design allows each motor to hover at a mere 60 W, enabling the use of high-density lithium-ion cells typically unsuitable for drone applications. The rest of the electronics are off-the-shelf, with the flight controller running ArduPilot. Due to the unconventional powertrain and large size, the PID tuning was very challenging.
We like the fact this drone doesn’t require fancy materials or electronics, it just uses existing tech creatively. The combination of extended flight times, rapid charging, and modular construction opens new possibilities for applications like surveying, delivery, and emergency response where endurance is critical.