Ore To Iron In A Few Seconds: New Chinese Process Will Revolutionise Smelting
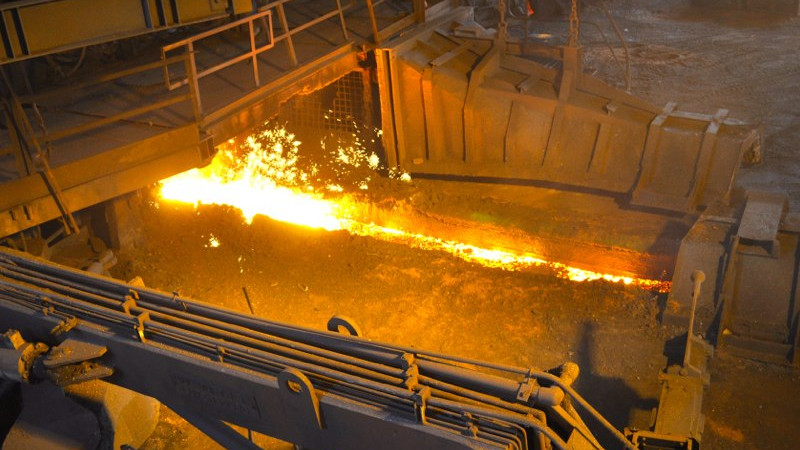
The process of ironmaking has relied for centuries on iron ore, an impure form of iron oxide, slowly being reduced to iron by carbon monoxide in a furnace. Whether that furnace is the charcoal fire of an Iron Age craftsman or a modern blast furnace, the fundamental process remains the same, even if the technology around it has been refined. Now details are emerging of a new take on iron smelting from China, which turns what has always been a slow and intensive process into one that only takes a few seconds. So-called flash ironmaking relies on the injection of a fine iron ore powder into a superheated furnace, with the reduction happening explosively and delivering a constant stream of molten iron.
Frustratingly there is little detail on how it works, with the primary source for the news coverage being a paywalled South China Morning Post article. The journal article alluded to has proved frustratingly difficult to find online, leaving us with a few questions as to how it all works. Is the reducing agent still carbon monoxide, for example, or do they use another one such as hydrogen? The interesting part from an economic perspective is that it’s said to work on lower-grade ores, opening up the prospect for the Chinese steelmakers relying less on imports. There’s no work though on how the process would deal with the inevitable slag such ore would create.
If any readers have journal access we’d be interested in some insight in the comments, and we’re sure this story will deliver fresh information over time. Having been part of building a blast furnace of our own in the past, it’s something we find interesting