The Lancaster ASCII Keyboard Recreated
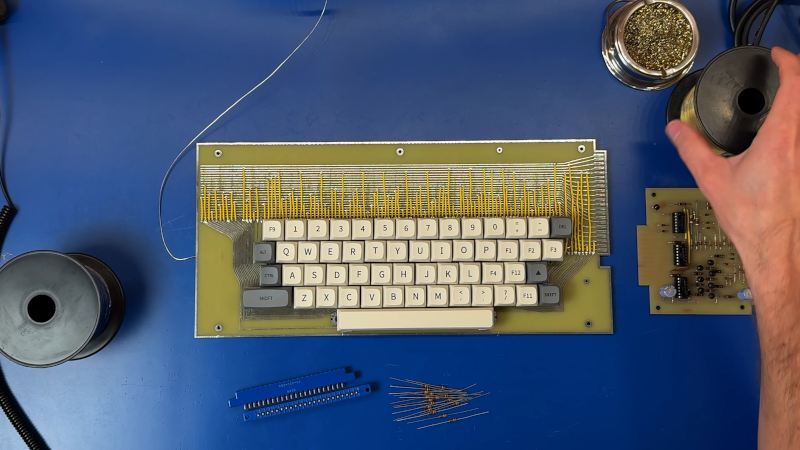
It is hard to imagine that there was a time when having a keyboard and screen readily available was a real problem for people who wanted to experiment with computers. In the 1970s, if you wanted a terminal, you might well have built a [Don Lancaster] “TV Typewriter” and the companion “low cost keyboard.” [Artem Kalinchuk] wanted to recreate this historic keyboard and, you know what? He did! Take a look at the video below.
The first task was to create a PCB from the old artwork from Radio Electronics magazine. [Artem] did the hard work but discovered that the original board expected a very specific kind of key. So, he created a variant that takes modern MX keyboard switches, which is nice. He does sell the PCBs, but you can also find the design files on GitHub.
Not only were the TV typewriters and related projects popular, but they also inspired many similar projects and products from early computer companies.
The board is really just a holder for keys, some jumper wires, and an edge connector. You still need an ASCII encoder board, which [Artem] also recreates. That board is simple, using diodes, a few transistors, and a small number of simple ICs.
If you weren’t there, part of installing old software was writing the code needed to read and write to your terminal. No kidding. We miss [Don Lancaster]. We wonder how many TV typewriters were built, especially if you include modern recreations.