A Unique Linear Position Sensor Using Magnetostriction
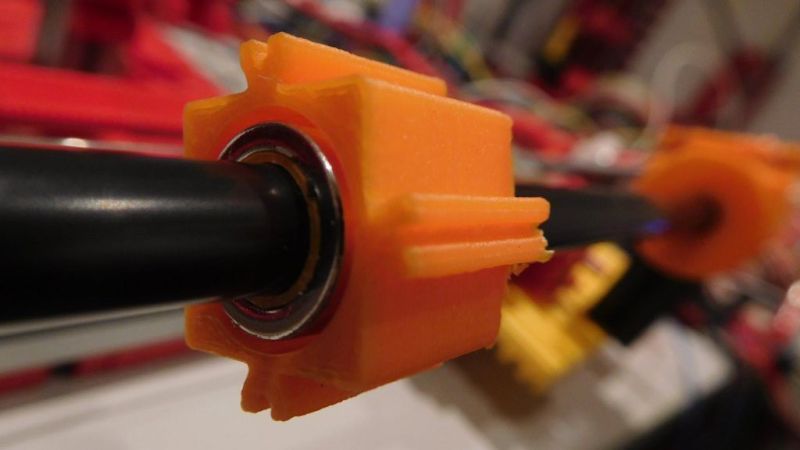
To the extent that you’re familiar with magnetostriction, you probably know that it’s what makes big transformers hum, or that it’s what tips you off if you happen to walk out of a store without paying for something. But magnetostriction has other uses, too, such as in this clever linear position sensor.
Magnetostriction is just the tendency for magnetic materials to change size or shape slightly while undergoing magnetization, thanks to the tiny magnetic domains shifting within the material while they’re aligning. [Florian B.]’s sensor uses a side effect of magnetostriction known as the Wiedenmann effect, which causes a wire to experience a twisting force if a current pulse is applied to it in a magnetic field. When the current pulse is turned off, a mechanical wave travels along the wire to a coil, creating a signal. The difference in time between sending the pulse and receiving the reflection can be used to calculate the position of the magnet along the wire.
To turn that principle into a practical linear sensor, [Florian B.] used nickel wire stretched tightly down the middle of a PVC tube. At one end is a coil of copper magnet wire, while the other end has a damper to prevent reflections. Around the tube is a ring-shaped cursor magnet, which can move up and down the tube. An exciter circuit applies the current pulse to the wire, and an oscilloscope is used to receive the signal from the wire.
This project still appears to be in the prototype phase, as evidenced by the Fischertechnik test rig. [Florian] has been working on the exciter circuit most recently, but he’s done quite a bit of work on optimizing the cursor magnet and the coil configuration, as well as designs for the signal amplifier. It’s a pretty neat project, and we’re looking forward to updates.
If you need a deeper dive into magnetostriction, [Ben Krasnow] points the way.